Fused Deposition Modeling (FDM), also known as Fused Filament Fabrication (FFF), is a popular and widely used 3D printing technology. This article will explore the intricacies of FDM 3D printing, covering its history, process, advantages, disadvantages, applications, and more.
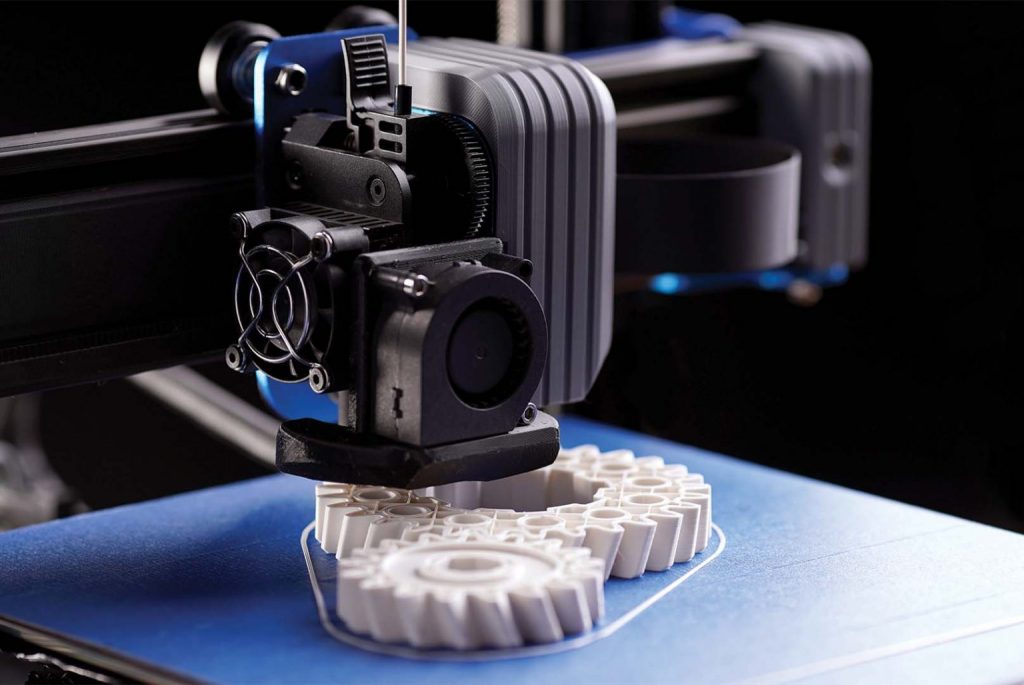
Source: HLH Rapid
History of FDM 3D Printing
FDM 3D printing was invented in 1988 by S. Scott Crump, co-founder of Stratasys. Crump’s initial goal was to find a faster method for prototype creation. He experimented with semi-solid plastics, melting them manually in layers using a glue gun. His first creation using this method, which he named Fused Deposition Modeling, was a toy frog for his daughter. The process was later automated with computer-aided manufacturing (CAM) software, and Stratasys began selling 3D printers for approximately $12,000.
With the expiration of the patent on FDM technology in 2009, its use expanded beyond Stratasys, leading to a significant decrease in prices and opening up opportunities for commercial, DIY, and open-source applications. However, it’s important to note that the term “FDM” itself remains a trademark owned by Stratasys. As a result, other companies often use the term “Fused Filament Fabrication” (FFF) or other registered names to refer to this 3D printing method.
How FDM 3D Printing Works
FDM 3D printing is an additive manufacturing process that involves building three-dimensional objects layer by layer from the bottom up. The process utilizes a continuous filament of thermoplastic material.
Here’s a step-by-step breakdown of the FDM 3D printing process:
- Design: A 3D model of the object is created using computer-aided design (CAD) software.
- Slicing: The 3D model is then sliced into thin layers by a slicing software, generating a set of instructions in G-code format.
- Printing: The FDM 3D printer heats the thermoplastic filament and extrudes it through a nozzle onto a build platform.
- Layer Adhesion: The extruded material bonds with the previous layer as it cools and solidifies.
- Building: The process of extruding and layering is repeated, following the G-code instructions, until the entire object is printed.
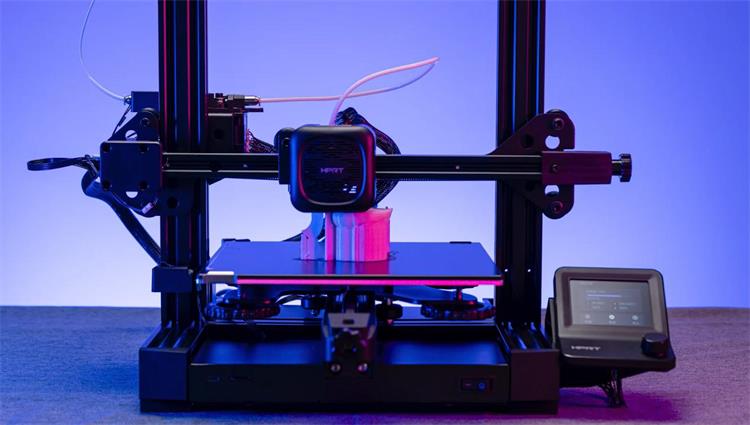
Source: HPRT
Materials Used in FDM 3D Printing
FDM 3D printing is compatible with a variety of thermoplastic materials. Some of the most common materials include:
- PLA (Polylactic Acid): A biodegradable and cost-effective thermoplastic that’s easy to print with but has low strength and durability. PLA is often preferred for its visual quality and ease of use, making it suitable for prototyping and hobbyist projects.
- ABS (Acrylonitrile Butadiene Styrene): A durable plastic used in various everyday items. While more durable than PLA, ABS can be more challenging to print and is more susceptible to warping.
- Nylon (Polyamide, PA): Known for its durability and strength, Nylon is often used in applications requiring robust parts, such as prosthetics and enclosures.
- PETG (Polyethylene Terephthalate with Glycol): A versatile thermoplastic commonly used in consumer packaging prototyping due to its practicality.
- TPU (Thermoplastic Polyurethane): Produces rubber-like parts useful for prototyping seals and gaskets.
Apart from these, more advanced materials like PEEK, PEI, and carbon fiber reinforced filaments are also used in FDM 3D printing in Malaysia, expanding its applications into demanding fields like aerospace and automotive.
Advantages of FDM 3D Printing
FDM 3D printing offers several advantages that contribute to its popularity:
- Cost-effectiveness: FDM is considered one of the most affordable 3D printing technologies, especially for prototyping and small-scale production. The materials used are also relatively inexpensive and readily available.
- Ease of Use: FDM printers are relatively simple to operate and maintain, making them suitable for both beginners and experienced users.
- Material Variety: FDM is compatible with a wide range of thermoplastic materials, offering versatility in terms of mechanical properties, colors, and finishes.
- Fast Turnaround: FDM printers can produce parts relatively quickly, with shorter lead times compared to some other 3D printing methods.
Disadvantages of FDM 3D Printing
Despite its numerous advantages, FDM 3D printing also has some limitations:
- Anisotropy: FDM-printed parts are anisotropic, meaning they exhibit different mechanical properties in different directions due to their layered structure.
- Visible Layer Lines: Due to its layer-by-layer printing process, FDM-printed objects often exhibit visible layer lines, which may require post-processing to achieve a smoother surface finish.
- Limited Detail and Accuracy: FDM struggles to produce intricate details and sharp corners due to the limitations of the extrusion process.
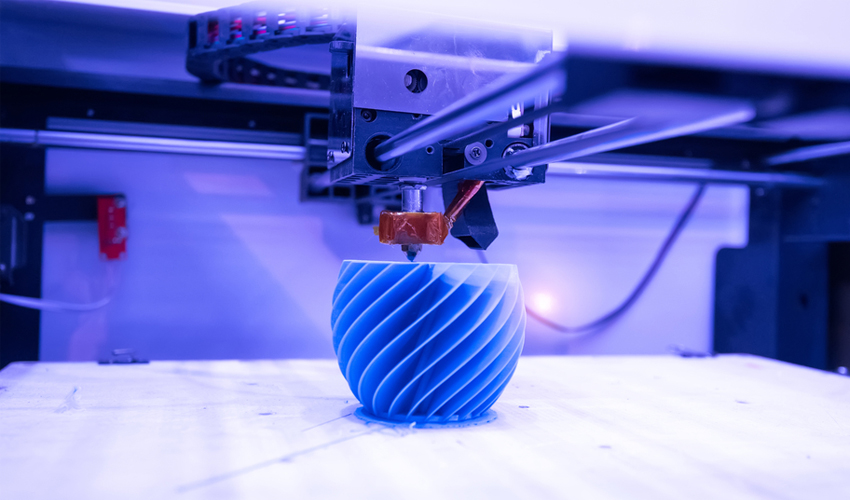
Source: 3D Natives
Applications of FDM 3D Printing
FDM 3D printing finds applications in a wide range of industries and fields:
- Prototyping: FDM is widely used for rapid prototyping due to its speed, affordability, and ability to create functional prototypes.
- Manufacturing: While traditionally used for prototyping, FDM is increasingly being adopted for low-volume manufacturing of end-use parts, jigs, fixtures, and tooling, especially in industries like aerospace and automotive.
- Education: FDM printers are becoming increasingly common in educational settings, providing students with hands-on experience in 3D design and printing.
- Medicine: FDM is proving valuable in medicine for creating custom prosthetics, medical models for pre-surgical planning, and even personalized medical devices.
Conclusion
FDM 3D printing is a versatile and accessible additive manufacturing technology that has revolutionized prototyping and is rapidly expanding its presence in manufacturing and other sectors. While certain limitations exist, its affordability, ease of use, and wide material compatibility make it a popular choice for various applications. As technology advances, we can expect to see further improvements in FDM 3D printing, leading to enhanced print quality, faster speeds, and even more innovative applications in the future.
Intrigued by the capabilities of FDM 3D printing? Dive deeper into the world of additive manufacturing with our comprehensive guides on resin 3D printing and SLA 3D printing. Whether you’re a hobbyist eager to refine your craft or a professional looking to optimize your production process, our articles provide detailed insights and comparisons to help you choose the best 3D printing technology for your needs.
Visit our website and contact us directly to learn more!